12 Benefits of Service Level Agreements for Food Processors
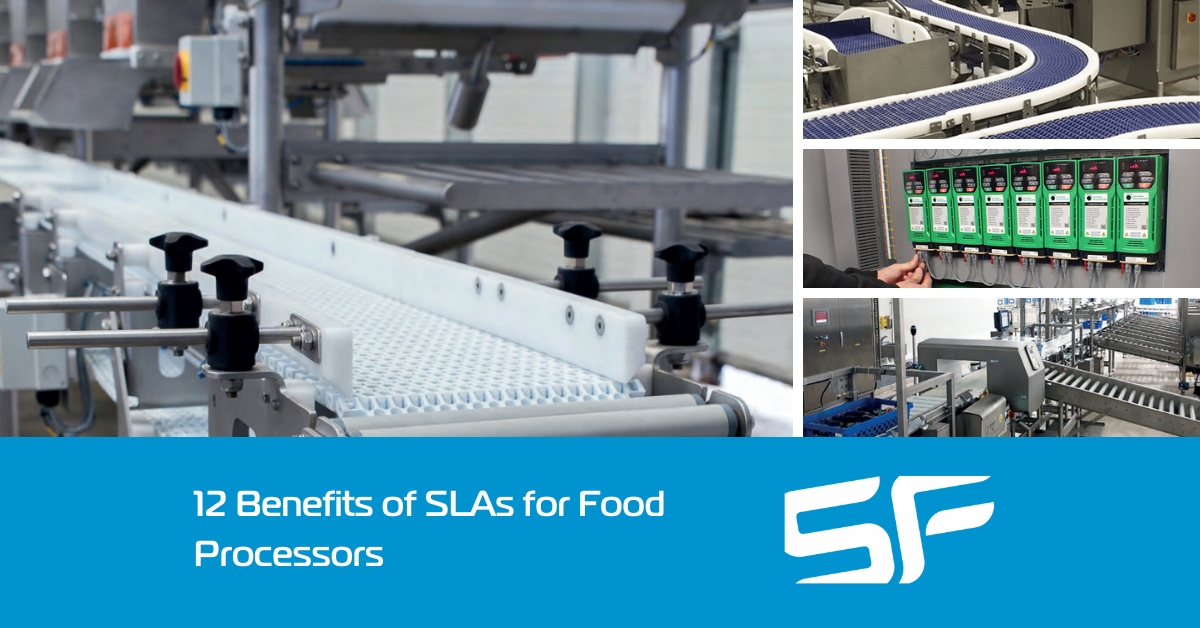
How you decide to handle the maintenance of the equipment on your food production lines will have a significant impact on your business. Two of the main options that are available are ad hoc maintenance and putting in place a Service Level Agreement (SLA). Here are 12 reasons why SLAs are the best approach for food processors.
1. Prevents Breakdowns and Unplanned Downtime While Optimising OEE
Equipment failures and unplanned downtime bring nothing but headaches to food production facilities. By putting in place an effective SLA, you will ensure the smooth and efficient running of your food processing equipment, while minimising wear and tear. This will minimise breakdowns and the dreaded unplanned periods of downtime, as well as optimising OEE – Overall Equipment Effectiveness.
2. Saves Money
The cost of an SLA is considerably lower than the costs you incur during periods of unplanned downtime. While actual costs vary from facility to facility, the total costs of equipment breakdowns can run into tens of thousands per day, particularly if the breakdown stops an entire production line. You could lose stock, orders can’t be fulfilled, you still have to pay staff, and energy costs remain ongoing. This is before you factor in the cost of the repair.
As SLAs prevent breakdowns and unplanned downtime, you will save money.
3. Optimise Your Budget and Control Operating Costs
Reducing the cost of maintenance and repair in your food processing facility is essential, but it is also beneficial to gain better control over your costs. While there will always be an unknown element, SLAs add a significant level of cost certainty, helping you control and optimise your budget.
4. Ensures Machines are Fully Calibrated
The machines on your production line need to operate within specified tolerances for reasons that include product quality, compliance, and line performance. The regular maintenance provided by an SLA will ensure the critical equipment in your facility remains properly calibrated and traceable to national standards.
5. Identify Potential Failures Early
The ideal situation with equipment maintenance is to:
- Only replace parts that need to be replaced
- Replace those parts before they reach failure point
An SLA will help you achieve this ideal maintenance situation as your equipment can be regularly inspected as part of the terms of the agreement. Those inspections will ensure good parts are not unnecessarily replaced, while also spotting components that are coming to the end of their usable life.
6. Optimises the Timing of Maintenance Work
There are good times to conduct maintenance in your food processing facility and there are times when it is costly and disruptive. With an SLA in place, maintenance can be properly planned to ensure it is carried out at an optimal time that minimises disruption. This is usually when the maintenance will have the least impact on production line output.
7. Fast Response
Response times are a crucial part of SLAs in the food industry. Not only will you get a guaranteed priority response time when you have an SLA, but the engineers that respond to your request will already have a good level of knowledge of your facility, lines, and equipment.
8. Improves the Service You Deliver to Your Customers
Optimising how you manage maintenance keeps your equipment and lines running as they should. This is central to maintaining your service standards, delivering on contractual requirements, and exceeding customer expectations.
9. Reduces Waste
Breakdowns and unplanned downtime often result in waste from lost product, contaminated product, and lost raw materials. As SLAs can prevent breakdowns and unplanned downtime, they can also help reduce waste.
10. Prevents Supply Chain Disruption
Unplanned downtime that reduces or stops production lines from running can have knock-on effects on your supply chain, both upstream and downstream. As supply chain management is a critical priority for many food manufacturing businesses, particularly in the current economic and geopolitical climate, minimising disruption is essential.
11. Prevents Lost Revenue
SLAs can prevent the lost revenue that can occur when your production line is not operational. It can also prevent lost revenue over the long term, as providing a reliable service and supply of products to your customers can help you retain contracts and orders.
12. Extends Machine Usable Life
Timely and effective maintenance helps to maximise the usable life of production line equipment. An SLA will ensure your equipment is maintained according to custom requirements and/or the manufacturer’s guidelines.
Arrange an SLA Today
At SF Engineering, we offer customised SLAs tailored to your production facility and specific requirements. We service and maintain a wide range of equipment from leading brands, including all equipment from our industry partners, whether supplied by us or a third party.
To discuss your requirements and find out more about the level of maintenance cover that we can put in place for your business, please contact us today. If you are in the UK, email servicesuk@sfengineering.co.uk. If you are in Ireland, email serviceandspares@sfengineering.ie.