12 Essential Considerations When Expanding Capacity and Optimising Food Production Lines
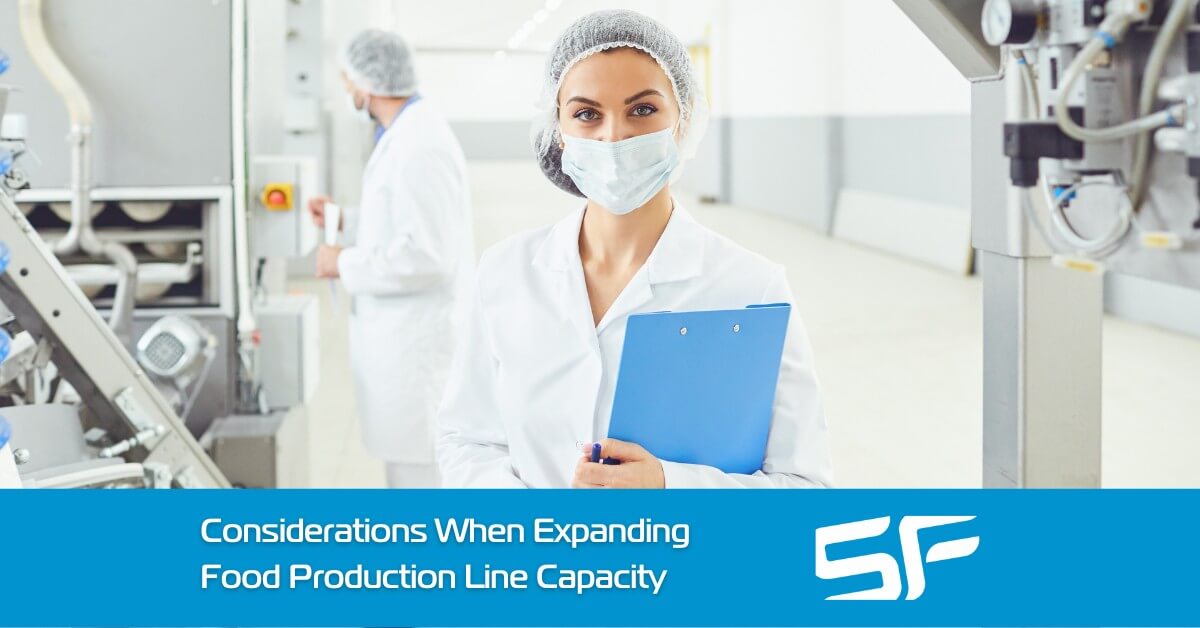
Continuous improvement and modernisation are essential for food manufacturers to stay competitive, address challenges in the industry (such as skills shortages), and meet the requirements of customers. As a result, many food processors are looking at expanding capacity and/or optimising processes.
Where is the best place to start and what should you aim to achieve?
How do you ensure a fast return on investment?
How do you mitigate and eliminate the risks that come with making significant changes to established factory layouts and operational production lines?
The following 12 considerations answer these questions while helping ensure your capacity expansion and process optimisation project is a success.
Partner Selection
The partner you select for the project will be crucial to its success, so it’s essential to choose a partner with as much in-house capabilities and expertise as possible. Some questions to look at include:
- Have they experience in delivering similar solutions?
- Do they specialise in food manufacturing equipment consultancy?
- Do they just offer design services, or do they manufacture in-house as well?
- Do they have a problem-solving track record and experience working on complex projects?
It’s also beneficial to choose a partner who can provide comprehensive services covering the whole project and who has full solution knowledge and expertise.
Defining Objectives
Defining your objectives for the project is a crucial step. This includes operational objectives such as the capacity level you want to reach or yield targets you want to achieve. Return on investment and business development objectives are also important.
Food Production Process
The food production process required to take the raw materials through to a finished product packaged and ready for dispatch is another essential consideration. Skilled and experienced design engineers will get a thorough understanding of this process to help them identify areas for improvement, efficiency savings, and automation.
Resource Availability
The resources and skills you have available will also be a critical factor in determining the direction the project takes and the final design and line layout that is developed. Recruitment and retention challenges, for example, might mean significantly increasing automation through an investment in new equipment.
Working Environment
The working environment pre- and post-installation is another important consideration as capacity expansion and process optimisation projects are ideal opportunities to improve the conditions for operators. In fact, improving working conditions might be one of your objectives for the project, and it can help with other considerations, including improving staff retention.
Physical Environment Characteristics
Getting a full understanding of the layout of the current factory and the size and characteristics of the available footprint are essential parts of the process. However, it’s also important to go beyond getting this understanding to also engage in out-of-the-box thinking so the available space can be efficiently used and fully utilised.
New and Existing Equipment and Technologies
What equipment will be retained on the production line or within the upgraded factory layout and what will be replaced? What new equipment will be introduced and what are the options that are available? What are the integration requirements and what data needs to be collected and communicated? Getting any new equipment properly specified by subject matter experts is also essential.
Compliance
Compliance considerations should be factored into the process every step of the way. This includes food safety compliance considerations as well as health and safety for workers and others in the facility.
Sustainability
Sustainability is a big consideration for manufacturers in the food industry and, crucially, their customers. Therefore, it’s important that sustainability isn’t treated as an afterthought. Instead, sustainability should be front and centre of all critical decisions.
Hygiene
Good equipment hygiene standards are important for a range of reasons including food safety, water use, chemical use, energy use, and the resources and time it takes to clean production line equipment. Everything possible should be done to maintain food safety, hygiene, and quality standards while minimising the water, materials, and time it takes to keep equipment clean.
Maintenance
Projects to expand capacity or optimise processes in food production lines should consider the full lifecycle of the line and the equipment that is installed. This includes the maintenance that is required, what that maintenance will involve, where the parts will be sourced, and who will complete the work.
Installation and Commissioning
The process for installing and commissioning the new or upgraded line should be considered at the very outset of the project. The objective should always be to reduce the impact that the installation and commissioning work will have on production to as close to zero as possible while achieving critical deadlines and milestones.
Support for Your Capacity Expansion or Process Optimisation Project
At SF Engineering, we have extensive experience designing, developing, manufacturing, installing, and maintaining food production lines that increase capacity and deliver significant process improvements. We offer end-to-end solutions, and we have the capabilities and expertise to ensure your objectives are achieved, even on complex projects. Get in touch today to speak to a member of our team.