How Service Level Agreements Save Food Processors Tens of Thousands of Pounds/Euros
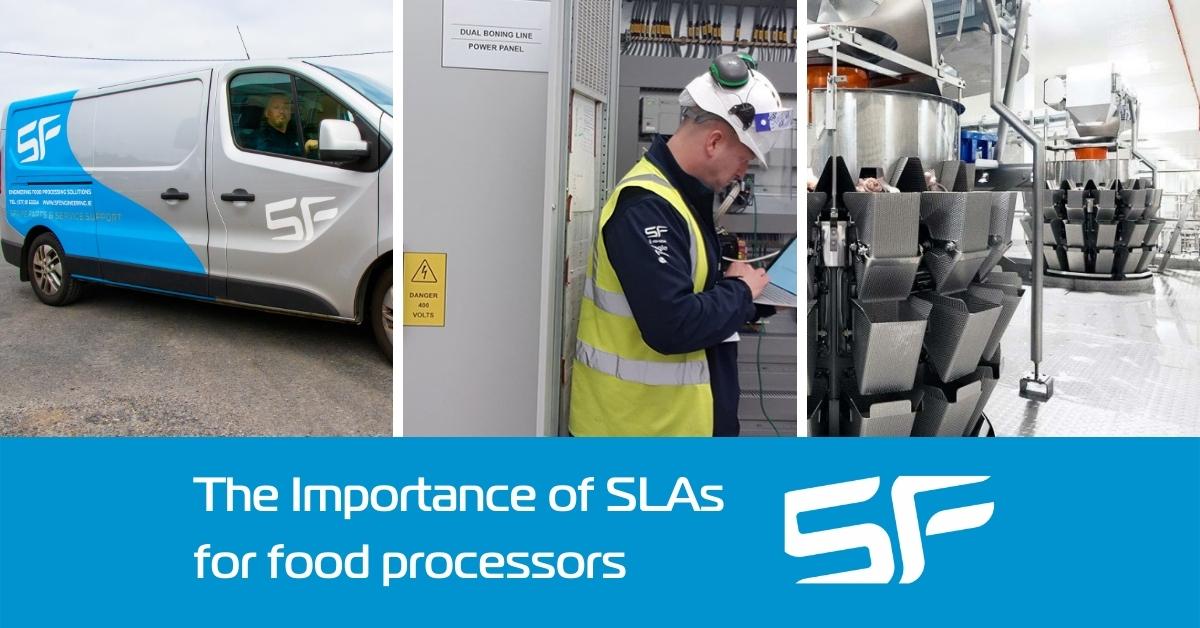
Production line downtime is part of running a food processing facility, whatever sector of the industry you are in, and whatever types of products you produce. Even though it is a normal part of food processing businesses, downtime can be hugely costly. A significant proportion of those costs can be eliminated with an SLA – a service level agreement.
Putting in place an SLA moves you from reactive maintenance processes to proactive maintenance, where you anticipate problems and keep equipment running as efficiently as possible.
And here’s the most important point – the investment you make in an SLA will pay you back multiple times each year.
Planned vs Unplanned Downtime
During periods of downtime, your food processing facility is not making money. Often this is unavoidable, such as during batch changeovers or scheduled maintenance. This is planned downtime.
Unplanned downtime is where large and often unavoidable costs are incurred. There are many reasons for unplanned downtime, but one of the most common is equipment failures.
During periods of unplanned downtime, you can’t manufacture products or deliver on the requirements of your customers. Your costs will increase at the same time, often by tens of thousands a day, as you lose money on waste, lost revenue, repair costs, and salary costs as your staff still need to be paid even when your production lines can’t operate.
How SLAs Minimise Unplanned Downtime
Many food processing facilities manage maintenance with a two-pronged strategy:
- Servicing equipment according to manufacturer guidelines
- Carrying out repairs whenever faults occur
In many cases, even the above is not always fully adhered to, as servicing dates can slip due to the needs of the business, and maintenance can be delayed.
That is before you take into account the relevance of manufacturer guidelines to your facility. The way you operate equipment could, for example, mean you don’t need maintenance as often as the manufacturer recommends. In other situations, it would be more cost-effective for you to service equipment more regularly.
SLAs take the above maintenance strategy to the next level by making maintenance proactive. So, rather than waiting for a generalised servicing date set by the manufacturer, servicing takes place according to the needs of your business.
SLAs also help to prevent faults from occurring as your equipment is proactively serviced and maintained.
The Benefits of SLAs for Food Processors
There are many benefits of putting an SLA in place to cover the equipment on your production line. The main benefits include:
- Ensures your food processing equipment runs as efficiently, smoothly, and effectively as possible
- Ensures machines are fully calibrated so they operate within desired tolerances
- Enables the continuous monitoring of equipment to identify failures as early as possible
- Prevents breakdowns and minimises equipment wear and tear
- Identifies many impending failures before they occur
- Facilitates essential maintenance work at times that have the least impact on production output
- Ensures you get a fast response to breakdowns by a team of engineers that have specific knowledge of your production lines and equipment
- Maintains customer service standards and commercial contract deliverables
- Reduces waste from lost raw materials when production lines are unavailable
- Also reduces waste from contamination or product damage caused by faulty equipment
- Helps with supply chain management
- Prevents lost revenue in the short-term through products not being produced and in the long-term through lost contracts and orders
- Extends the usable life of food processing equipment
- Maximises uptime and OEE
- Helps control operating costs
Return on Investment
In addition to understanding the benefits of SLAs, it’s also worth considering return on investment, as an SLA is more than a simple cost to your business. In fact, the cost of an SLA is often offset by a reduction in annual repair costs. This is before you even take into account reductions in other costs, such as lost revenue, retailer fines, or lost contracts.
SF Engineering’s SLAs
At SF Engineering, we offer comprehensive and fully tailored SLAs for food processors in the UK and Ireland. We have extensive experience in the industry, and we have the expertise to service and maintain equipment whether it was designed by us or not.
Your tailored SLA could cover a set number of engineering days per year, for example, or it could involve quarterly or six-monthly inspections of your equipment. We also typically include annual stripping and maintenance of equipment in our SLAs.
When issues are identified, we’ll then make a recommendation on what needs to be done, providing you with a discounted cost for parts and a quote for the repair.
To discuss putting in place an SLA for your food processing facility, or for any other maintenance or repair query, please get in touch with us at SF Engineering today.