Optimising Food Manufacturing Facilities: SF Engineering’s Consultancy Expertise and Capabilities
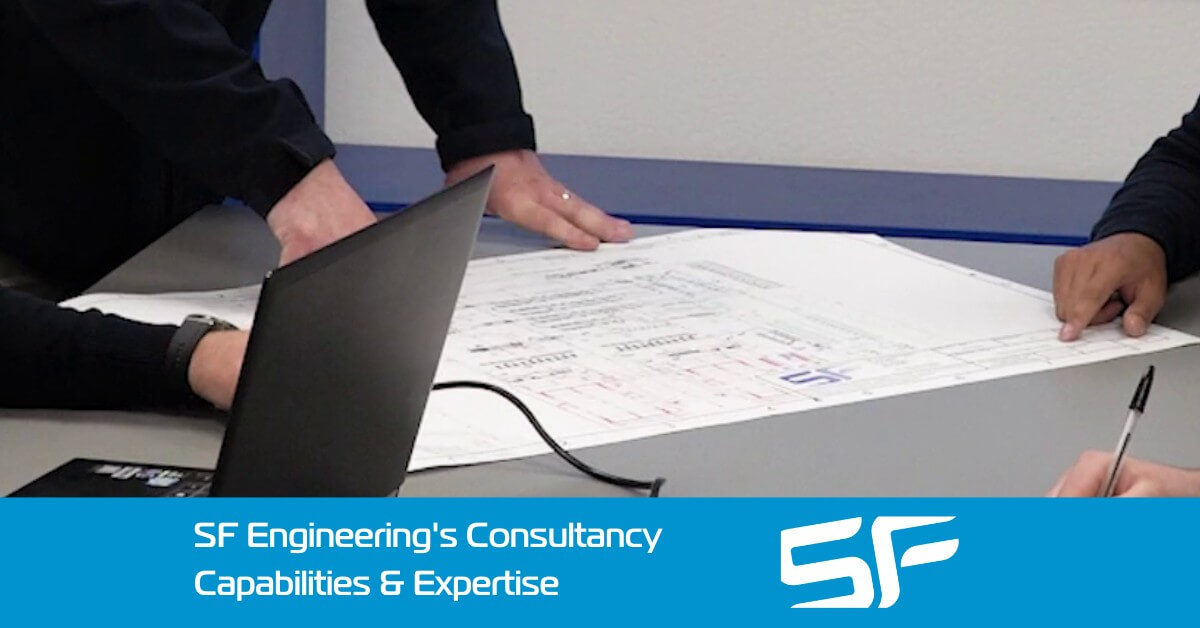
In the first part of this two-part blog series, we looked at the growing importance of consultancy to the success of food production line optimisation projects. In summary, working with food processing equipment experts on a consultancy basis from the earliest possible stages ensures the project starts from the right starting point and follows a clear direction of travel. The success of all other aspects – design, planning, project management, manufacturing, installation, and commissioning – all flow from the initial consultancy phase.
In this second blog of the series, we will look at the expertise that is required from your equipment solution partner, as well as our capabilities at SF Engineering.
Essential Expertise for the Consultancy Phase of Your Project
Listening, Observing, Analysing, and Understanding
One of the first things that needs to be done in the consultancy phase is to get a full understanding of your current processes, equipment, and workflows. It’s important to know what is working well and what is causing serious challenges and bottlenecks. Having a detailed understanding of the product/s produced on the line/s is also beneficial. Our extensive prior experience and knowledge of fresh food production environments and processes significantly enhance the understanding and analysing phase.
Defining Objectives
Defining your objectives and what you want to achieve is also crucial, whether you are modernising the facility, expanding capacity, or optimising processes. There should be both technical objectives (throughput, yield, process automation) and business objectives (ROI, cost savings, staff retention, etc).
Often the business ROI can come as much from improving product flows, reducing manual handling, and eliminating unnecessary movement and non-value-adding tasks as it does from adding a piece of automation.
Full Solution Knowledge
Your solution partner should have in-depth knowledge of all critical factors that will influence the project as it progresses. Examples include:
- Design, planning, project management, manufacturing, equipment integration, software configuration, installation, and commissioning.
- Developing solutions where the available footprint is limited or otherwise challenging.
- Factory layout, technology, equipment capabilities, and packaging options.
- Available technologies and equipment, from weighing and grading to conveyors and quality control.
- Food production line staffing considerations, including skills availability, workstation ergonomics, efficiency, safety, recruitment, and retention.
- Process and control automation, as well as mechanical and electrical services.
- Health and safety as well as food safety and regulatory compliance expertise.
- Food production line processes relevant to your industry, from raw material intake processes to end-of-line processes.
- Sustainability, including energy efficiency, water use, and waste.
- Post-installation considerations, including maintenance, cleaning, and hygiene.
The above expertise aids with problem-solving and decision-making to help progress the project to the design, planning, manufacturing, and equipment specification stages.
SF Engineering’s Consultancy Capabilities
SF Engineering will bring a full range of food processing solution consultancy services to your project. This includes layout development, engineering design, and both technical and financial feasibility studies.
We can also optimise our approach based on your objectives. Examples of common objectives include:
- Increase throughput and yield, including in situations where there are limitations on available floor space.
- Improve working conditions for operators to increase productivity and help with recruitment and retention.
- Optimise flows on the production line and within the wider factory environment.
- Minimise manual handling.
- Eliminate bottlenecks on your production line/s.
- Reduce manufacturing costs.
- Reduce product giveaway or improve yield.
- Improve product quality and presentation.
- Enhance sustainability.
- Improve hygiene.
Full Range of Services
At SF Engineering, we’ll bring over 40 years of in-house experience to your project with a team of dedicated, innovative, and knowledgeable professionals. We’ll also work closely with our industry-leading equipment partners to develop a fully optimised solution.
To arrange an initial consultation on the factory improvement or modernisation project that you are planning, please get in touch with us today and a member of our team will get back to you.